Processes During Manufacturing
Grains Cleaning Process
Cleaning is one of the last operations of the harvesting process. Cleaning grain means removing all the materials other than the grain. This could be sand, stones, straw, weeds and so on.
Grain cleaning after harvest is important as it removes unwanted materials from the grain. Clean grain has a higher value than grain that is contaminated with straws, chaff, weed seeds, soil, rubbish, and other non-grain materials.
Grain cleaning will improve the ability of the grain to be safely stored, reduce unwanted materials (dockage) for milling, and improve milling output and quality. Dirty grain can attract certain insects or fungus that might damage the grain. Seed cleaning: Malformed, discolored, germinated, broken or moldy grains in seed lots can severely impact seed quality, viability and vigor. Visually inspect the seeds prior to storage and remove these grains from the seed lot.
In most cases, the raw materials delivered to the mills are not pure grains. Prior to their processing, foreign materials and other contaminants introduced during the harvest, transport and storage of the grain must be removed. The removal of such impurities guarantees the quality of the products, by reducing ash content, specks, and factors influencing flavour. Additionally, machine wear is reduced and their lifespan increased.
Trilokpati having Buhler USA grain-cleaning machines separate defects from grains with maximal precision based on variable physical properties: size, magnetic response, equilibrium velocity, density, length, shape, firmness and colour. An effective and consistent means of regulating the grains’ moisture levels is an important follow-up to their cleaning. For this, our plant have systems for the automatic regulation of moisture levels, comprised of moisture level measurement, calculation of flow rates, water dispensation and its distribution over the grain surface.
Optical Sorting (Safe Food. Clean Food.)
An optical sorter is a device that automatically sorts objects based on visual criteria. Also known as sorting machines, optical sorters are often found in manufacturing and food processing facilities. They are used to find defects and separate different types of items. There are several different types of sorters including some that make use of light sensors while others use infrared light.
Trilokpati having Buhler Sortex is the world leader in innovation and delivery of optical sorting solutions to the global food and non-food processing industries.
Trilokpati Plant can sort a variety of grains, beans, pulses, spices, nuts, rice, vegetables and fruits as well as non-food products such as plastics by colour and shape with accuracy and efficiency.
Colour, size and shape optical sorters
Trilokpati Plant having optical sorters leverage a range of innovative technologies like high definition custom-built cameras, InGaAs technology, Profile technology, high-pressure ejectors and optimised feed mechanisms to achieve highest yield and unmatched quality of products.
Sifting & Grading
The sifting principle is based on a circular movement of a sieve, which separates small and light particles from small, but heavy particles.
Trilokpati having Buhler offers a wide range of solutions for the sifting and grading of floury products in wheat, rye, maize (corn), and durum mills as well as for the sorting of different bulk products. Systems for sifting and grading are characterized by high sifting capacity in a minimum space, excellent sifting efficiency, high sanitation and easy access for cleaning.
Agriculture
Vegetables
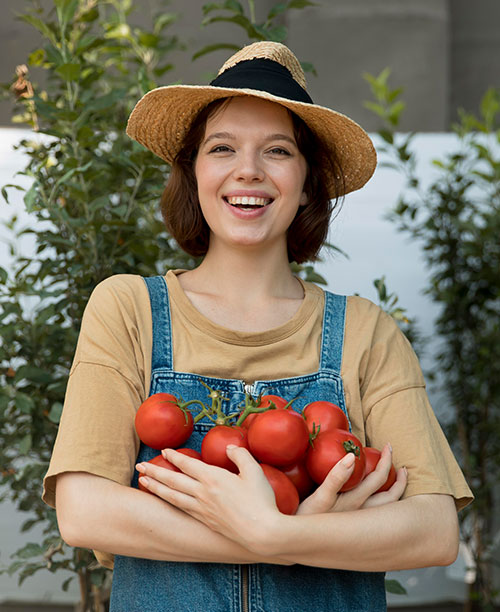
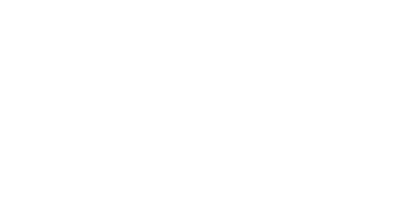
Special Care For Our Grain
Discount Options

Best Return Policy

Online Support
